Page 10 of 23
Posted: 01 Sep 2013, 11:44
by Zifle
matt3o wrote:yes, grouping is by thickness.
the base is steel, right? 1.5mm is still threadable I think if you do it right. consider that 3mm stainless steel is pretty hard to thread.
edit: unless you use an alu 3mm base of course
I asked my dad (he's the one with the tools), and he said 3mm steel shouldn't be a problem. If it ends up being all too difficult, I'd just drill the hole out, and use a nut on the other side. So 3mm steel base is my preference (and for the record, all of my layers should be steel, including the plate

)
Posted: 01 Sep 2013, 11:51
by Muirium
The steelers are coming out of the, uh, metalwork!
Posted: 01 Sep 2013, 12:05
by matt3o
Muirium wrote:There's a thought. What's a rough guess for much those bottom side layers (between the mezzanine and the base) will cost? I might have them made anyway, as a backup, with acrylic as my experiment.
the price impact of those two layers is really minimal (€5-10 I guess).
Posted: 01 Sep 2013, 12:09
by Muirium
Right, count me in for them in steel. It's a good Plan B.
Why are Photeq's stabs so different to everyone else's? Is he using Cherry stabs instead of Costar or is there something else I don't understand?
Posted: 01 Sep 2013, 12:15
by matt3o
okay guys. the original plan was to use:
1 sheet of 1.5mm aluminum for the plates
1 sheet of 3mm aluminum for the sides
1 sheet of 1.5mm steel for the bases or plates
That would help reduce the cost. Basically we don't have 3mm steel sheet. If you really want it I can add a 3mm steel but that would impact pricing on others having 3mm aluminum.
PS: Photekq stabs are cherry (actually I think it's universal, he can use costar as well), yes.
Posted: 01 Sep 2013, 12:19
by Muirium
I'd prefer 3 mm steel than aluminium. So Zifle wouldnt be entirely alone.
Posted: 01 Sep 2013, 12:57
by Zifle
matt3o wrote:okay guys. the original plan was to use:
1 sheet of 1.5mm aluminum for the plates
1 sheet of 3mm aluminum for the sides
1 sheet of 1.5mm steel for the bases or plates
That would help reduce the cost. Basically we don't have 3mm steel sheet. If you really want it I can add a 3mm steel but that would impact pricing on others having 3mm aluminum.
PS: Photekq stabs are cherry (actually I think it's universal, he can use costar as well), yes.
If there's not a significant price difference, and it helps with organization, and price for the rest of the buy, I don't mind going alu for the case, and then just steel for the plate, but other than that, I'd still prefer the full steel. In any case, it's not THAT big of a deal to me. Most important part is that the layers are 3mm, so I actually have the right height to work with.
So yea, if it's an issue, and I'd be the only one, I can easily just go with 3mm alu, but if Muirium is going with it regardless, so it's not an issue to include mine as well, that's my preference.
Posted: 01 Sep 2013, 13:07
by Muirium
Indeed. I'd prefer all steel too, but I don't need it badly enough to screw everything up.
It's consistency I want more than a particular material. Besides my mirror plate!
One form of consistency is for my design to be a double deck steel sandwich with an aluminium filling. Steel plate : aluminium sides : steel mezzanine : aluminium sides : steel base. That's the current idea I suppose!
Posted: 01 Sep 2013, 14:37
by Muirium
I finally figured out how to get dimensions out of .dwg files in DraftSight! (Yes, I'm slow.)
So the angle of my stepped case is determined by the triangle ABC:
Code: Select all
<---------------------------- Overall Depth (d) ----------------------------->
+----------------------------------------------------------------------------+
| Upper deck height (u) |
| A---------------------------------------B
| | Lower deck height (l)
+------------------------------------C
<------- Mezzanine Depth (m) -------->
d = 101
m = 50.5 <-- Currently the mezzanine is 50:50, at 101/2
u = 12 (3 layers of 3 mm plus 2 layers of 1.5)
l = 7.5 (2 layers of 3 mm plus 1 layer of 1.5)
The angle I'm interested in is ABC
tan ABC = AC / AB = l / d-m = 7.5 / 50.5 = 0.148514851485
ABC = 8.5 degrees
Just got out a protractor and measured a couple keyboards. (An Apple Aluminium and a Model M.) They both look about 7 degrees, or a sliver under, in their incline, measured at the side of the case. I use all my keyboards sitting flat, without feet extended, so this angle is quite important to me. I'll do some more measuring…
I might push back that split in the mezzanine a bit. There's a lot of room in there!
Posted: 01 Sep 2013, 15:59
by matt3o
consider that you can reduce the angle with the feet.
Posted: 01 Sep 2013, 16:07
by Muirium
True. I just want it as low to the desk as it can get. 6-7 degrees looks like what I'm used to. I'll figure something out.
By the way, opposite the USB hole, there's a similar reduction in thickness in the bottom side layers' corner wall. As in: top left = USB hole. Top right = what? I don't get it. The switches should all be cosy upstairs.
Moving the step back:
10 mm = 7.1 degrees
15 mm = 6.5 degrees
That's the zone I'm interested in! So instead of the split at 50.5:50.5 mm, does 35.5:65.5 work?
Yes, I'm haggling over half a degree here!
Posted: 01 Sep 2013, 16:14
by matt3o
Muirium wrote:As in: top left = USB hole. Top right = what?
for the sake of symmetry
Posted: 01 Sep 2013, 16:19
by Muirium
Right. I do indeed like that. I'm not sure about strength, though.
Posted: 01 Sep 2013, 16:32
by matt3o
Muirium wrote:Right. I do indeed like that. I'm not sure about strength, though.
once closed and screwed you can use it to cut diamonds. only issue might be during shipment, but my nuclear winter safe packaging is famous all over Europe.
Posted: 01 Sep 2013, 17:02
by Muirium
All right, there's 25.55 mm of open space in the lower deck, so to speak. (At its narrowest point. It's 46.5 mm elsewhere) I'd like to push 10 mm into that, so the step is a shallower angle.
A new .dwg and .pdf of this (plus the feet holes) to review would be splendid!
Posted: 01 Sep 2013, 17:20
by matt3o
you want to reduce the box to 36.5mm? you know that the 1.2a and 2a batteries are about 40mm?
Posted: 01 Sep 2013, 17:23
by Muirium
Sneaky…
Posted: 01 Sep 2013, 17:31
by matt3o
I just checked my 1a battery is actually 35mm, the power module 37mm. your call here. more room is always preferable but if you really need a smaller step I can reduce it.
Posted: 01 Sep 2013, 17:36
by Muirium
Presumably these guys are too big and/or too high in voltage:
http://en.wikipedia.org/wiki/9-volt_bat ... ifications
Posted: 01 Sep 2013, 17:44
by matt3o
I'm more talking about these
https://www.sparkfun.com/products/8483 (the 2a actually is 54mm)
Posted: 01 Sep 2013, 17:45
by mtl
matt3o wrote:I'm now waiting for mtl's new design (hurry up pal!)
Ok! I'll have it ready shortly.

Posted: 01 Sep 2013, 18:01
by Muirium
I like the look of this one!
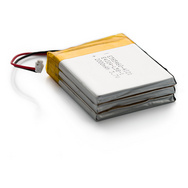
Anyway, point taken. That space is better off uncompromised. Thanks for thinking ahead.
Posted: 01 Sep 2013, 19:31
by matt3o
I updated the DWG in the first post. This is the preview.
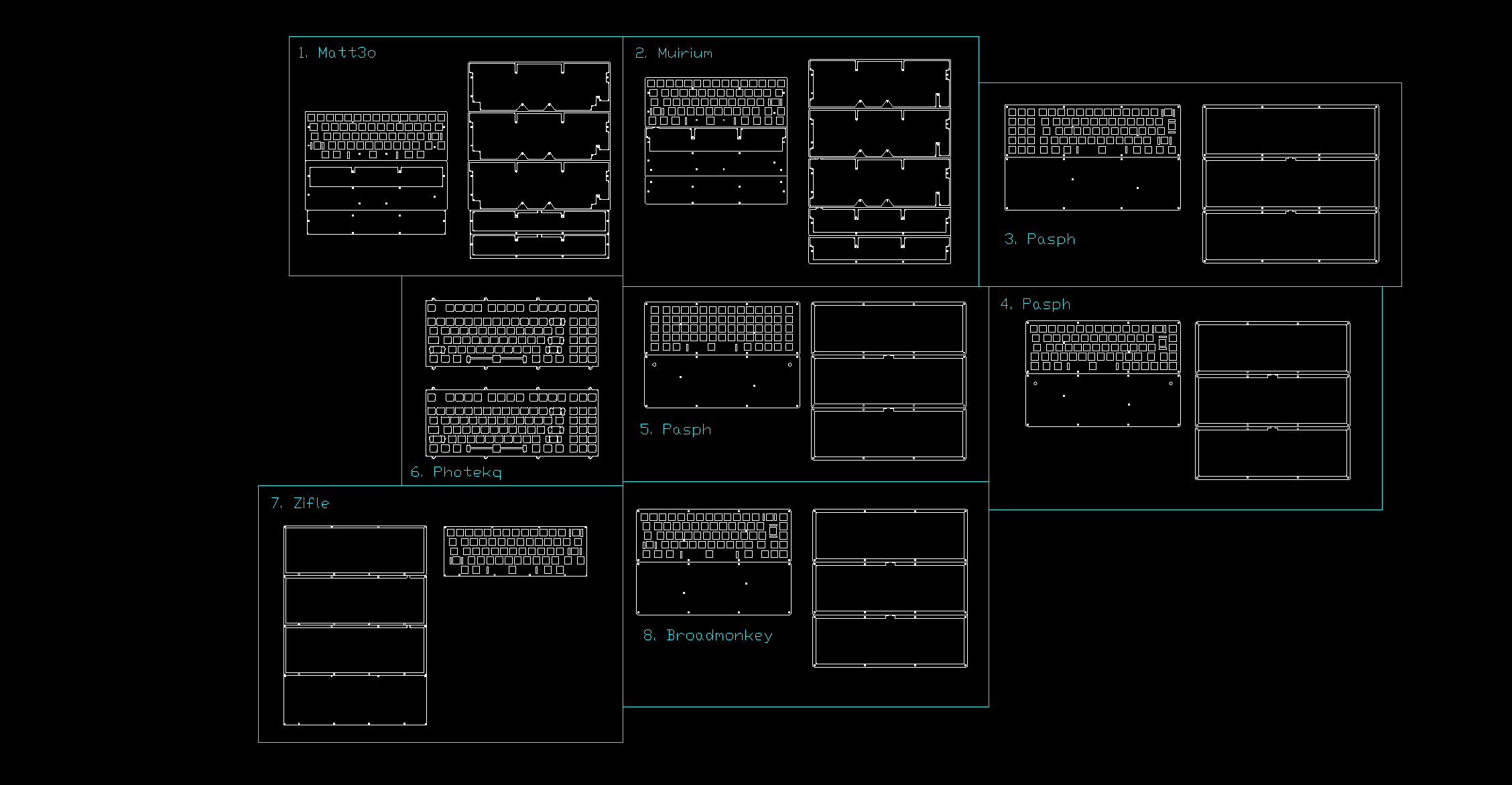
- final.png (25.28 KiB) Viewed 4223 times
Posted: 01 Sep 2013, 22:55
by mtl
My final design is attached.

Hope I'm not too late!
If you see any errors matt3o, please let me know.
For the 3mm layers, either aluminum or steel is fine, but I would prefer steel if it's significantly cheaper.
Posted: 01 Sep 2013, 23:47
by matt3o
thanks for reviewing it, mtl. You are totally on time

Tomorrow I'll post the final DWG.
Posted: 02 Sep 2013, 02:31
by mtl
Awesome! So glad I didn't miss the boat.
Here's an update without the risky IBM logo. Went with a version of the glider emblem instead:
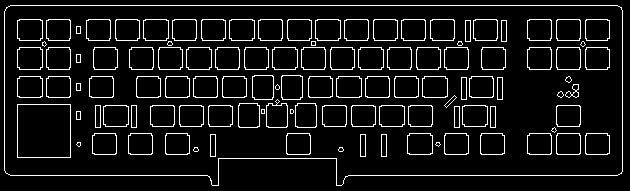
- top.png (4.02 KiB) Viewed 4169 times
Posted: 02 Sep 2013, 09:58
by matt3o
Okay now Muirium, Zifle and mtl want steel sides.
The goal of the GB was to use as much as possible the aluminum sheet (the 3mm one especially), this is not going to happen if we split the sides in alu and steel.
If everyone wants steel sides we can get rid of the 3mm alu altogether, but I thought this was a closed argument. The saving in such a small GB would be small anyway, so that's not really a issue (at least for me). Consider that steel is heavier so more expensive to ship.
So the options are:
1) everyone orders whatever he wants, no discount from the GB but everyone's super happy
2) everyone gets steel sides, small discount from the GB, slightly cheaper to cut, more expensive to ship
3) everyone gets alu sides, moderate discount from the GB, slightly cheaper to ship
This week I'm sending the order, if you don't make up your mind I'll board without you

Posted: 02 Sep 2013, 11:00
by Zifle
My stance is the same as previously, I don't mind going alu for the sides, but my preference is in steel. In any case (haha), I'd prefer the whole board to be of the same material, so whether it be steel or alu, doesn't matter too much for me, but I'm certainly not frightened by the weight (that's one of the reasons to go for steel!), and that adding to the shipping. After all, this gb IS moreso to get whatever we want cut, and not so much for saving cash, so that should be considered as well.
But for the last time, my stance is steel > alu, but I don't mind the latter, if that's what we end up with.
Posted: 02 Sep 2013, 11:15
by Muirium
The best way to settle this would be to submit two jobs for a quote: Matt's options 1 and 3 above: everyone's free choice vs. all aluminium for the 3 mm layers. Then we would know the actual number we're haggling about.
So long as we don't scare the cutters off again!
Posted: 02 Sep 2013, 11:38
by matt3o
Zifle wrote:My stance is the same as previously, I don't mind going alu for the sides, but my preference is in steel. In any case (haha), I'd prefer the whole board to be of the same material, so whether it be steel or alu, doesn't matter too much for me, but I'm certainly not frightened by the weight (that's one of the reasons to go for steel!), and that adding to the shipping. After all, this gb IS moreso to get whatever we want cut, and not so much for saving cash, so that should be considered as well.
But for the last time, my stance is steel > alu, but I don't mind the latter, if that's what we end up with.
you can have the steel plate, no problem with that since we already have the bottom in the same thickness (but you want it 3mm right?).
The visible part of the sides is just the section of the laser cut sheet, so (imvho) there's no real difference in doing that steel or alu.
Anyway let's see what others say.
Muirium wrote:The best way to settle this would be to submit two jobs for a quote: Matt's options 1 and 3 above: everyone's free choice vs. all aluminium for the 3 mm layers. Then we would know the actual number we're haggling about.
I would really like to avoid that.
A small full steel case should be around €80
A small full alu case should be around €140
The better we use the alu and steel sheets the lower the price, but to which extent is hard to say. I may predict a €10-20 saving.